Unseen Objects
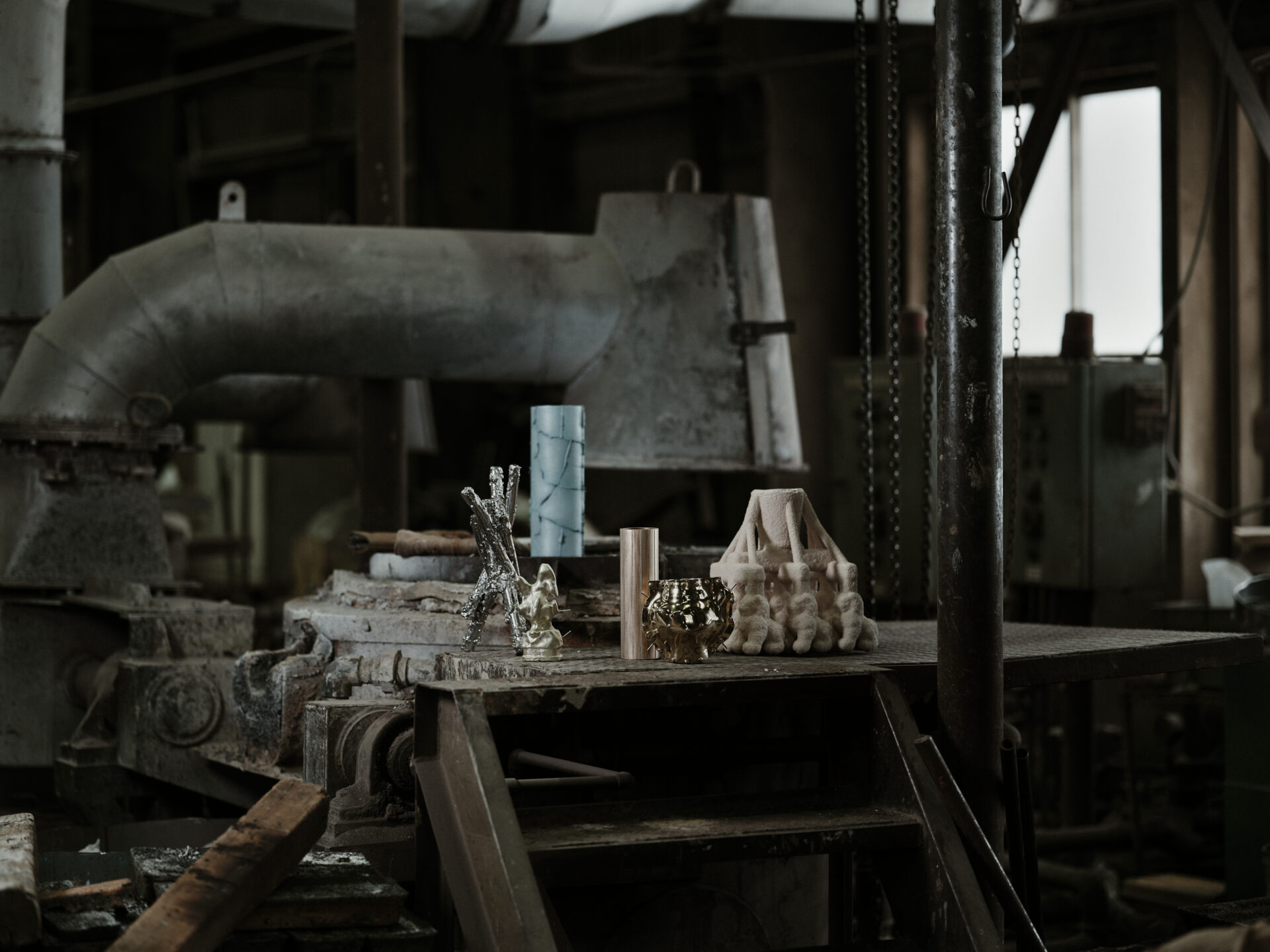
Redefining the Appeal and Value of Casting Culture
Unseen Objects is a collection of vases born from a collaboration between we+ and Heiwa Gokin, a foundry based in Takaoka, Toyama Prefecture. This collection reinterprets the tools, fixtures, material textures, and incidental forms found within the casting process—elements that have often been overlooked. By elevating the essence of advanced casting techniques into art, the collection seeks to highlight the inherent beauty of casting culture while simultaneously rediscover and redefine the value of casting craftsmanship, offering a fresh perspective on this time-honored tradition.
Project Details
Collection
Focusing on the overlooked uniqueness within the casting process
Takaoka city has been known as a center of casting copperware for over 400 years since the Edo period, with traditional techniques passed down through generations. It is also the only copperware production area designated as a traditional craft site by Ministry of Economy, Trade and Industry in Japan. Among them, Heiwa Gokin, established in 1906, has leveraged its expertise in casting and craftsmanship to produce a diverse range of works. From large-scale bronze statues, monuments, and religious artworks to delicate small sculptures and art pieces crafted using the lost-wax casting method, the company has continually refined its techniques to push the boundaries of metal casting. For this project, we+ made multiple visits to Heiwa Gokin’s factory, conducting an in-depth study of the casting process. By focusing on the overlooked beauty that emerges in daily operations, we created a collection of vases consisting of six unique pieces that capture and reinterpret this hidden aesthetic. These include: Casting Core, Rubber Mold for Lost Wax Casting, Ceramic Mold for Lost Wax Casting, Sand Residue, Burr, and Iron Rod for Core Structure of Sand Mold.
Casting, at its core, is an act of transformation, which includes a considerable layer of pragmatism combined with storytelling – blending chemistry, materiality, and craft in the direction of creating something new to be revealed. Casting is some sort of roller-coaster where you try to control a material and a practice, following a precise method, with the awareness that results could be still unpredictable.
Design Curator and Author, Maria Cristina DideroIn an era fixated on perfection, Unseen Objects offers a compelling counterpoint. The exhibition delights in the “mistakes” and “leftovers” of manufacturing: burrs that form where molds meet, sand that refuses to let go, and the intricate grids of reinforcement bars. Each piece reveals that beauty doesn’t have to be polished or pristine – it can reside in cracks, residues, and the marks of making. But this true exhibition delights consist not only in material exploration but it talks also about us, showing in the face our take on failure, our trials and errors which finally express our attitude toward life.
Casting Core
A ‘casting core’ is the mold inserted into a casting to create a hollow space within the metal object. Since it is not visible from the outside, craftsmen usually create casting cores as needed on the spot. These cores often have softened shapes with more smoothed edges compared to cast metal. For this project, we aimed to create a vase that embraces the unintended and ambiguous forms of these cores, preserving their distinctive characteristics.
Rubber Mold for Lost Wax Casting
In the metal casting technique known as ‘lost-wax casting’, rubber or plaster molds are created from a master model made of resin or metal. The inside of these molds is then carefully crafted to replicate the form of the model, whilst the exterior is shaped by hand by craftsmen to accommodate clamps and other tools used during the process. In this project, we faithfully reproduced the functional forms which were created for process efficiency and crafted them into vases.
Ceramic Mold for Lost Wax Casting
The ceramic mold used for lost-wax casting is created by alternately layering fine sand and coarse sand, which is then fired to undergo a ceramic transformation. When casting a large number of small objects or parts, various channels are created in the wax mold to ensure the metal poured from the top flows evenly throughout the master model underneath. In this project, we preserve and repurpose the sand molds which are destined to be destroyed once the product is complete, to create a new series of vases.
Sand Residue
After casting, the cooled cast object is removed from the mold with some sand remaining attached to it. This is known as residual sand, typically removed using vibration or an air gun. In this project, we intentionally left the sand on the cast object, to create a new form of casting where metal and sand are fused together.
Burr
When casting large metal objects, sand molds are divided into smaller sections according to the shape and size of the original model. When molten metal is poured into these molds and solidifies, burrs naturally appear in the gaps between the parts. Normally, burrs are removed during the finishing process, however, in this project, we create a vase that embraces the natural forms of burrs that emerge during the casting process.
Iron Rods
When casting large metal objects, sand molds are secured with frames made of iron rods to support their weight. Craftsmen weld the iron rods to create custom frames tailored to the specific object being cast. The iron rods, often reused multiple times, become bent and retain organic welding marks. In this project, we propose a vase that incorporates and highlights the distinctive shapes of these iron rods, showcasing the unique traces of the casting process.